Tar i bruk det gamle ELKO-bygget på Åmot for å lage nye plastdeler
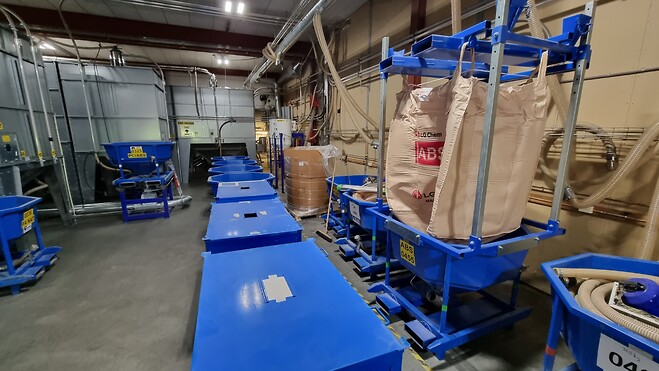
HEMMLIGE PLANER: Eiendomsfirmaet Asp Eiendom har kjøpt lokalene etter ELKO, selve kjøpet ble offentliggjort desember 2022, enda får vi ikke høre så mange detaljer om hva slags plastdeler som skal støpes i fabrikken.
Hva slags plastdeler og til hvem vil trolig ikke røpes før til høsten – eller tidlig i 2024. Men det som har skjedd til nå, er at Asp eiendom fra Oslo har forhandla seg frem og kjøpt fabrikken og arealet rundt.
– Sammen med Asp eiendom, har vi danna et nytt firma med navnet Sporpind Eiendom AS, forteller Svein Roger Reberg, ny del-eier med spennende planer.
Bruker de samme maskinene som laget stikkontakter
I den gamle Elko-fabrikken er det mange maskiner som produserer plast og kan støpe nesten alle plasttyper. På Elko-fabrikken laget de all plasten til stikkontakter, brytere og koblingsbokser og forskjellig annet.
Plastproduksjonen er fordelt på ca 1.500 kvadratmeter.
Fortsatt jobber gründerne med konkrete avtaler med eksterne om kjøring av maskinene for tilvirkning av plastdeler. Det er uansett avklart at de samme maskinene som stikkontaktene tidligere ble laget på, nå skal lage andre deler.
Reberg har jobbet i Elko i 27 år, se mer info på Linkedin om hva han har gjort. Allerede fra 2020 begynte han å jobbe med Elko og Schneider for å få tatt over mesteparten av maskiner og utstyr når tiden var inne for at fabrikken skulle legges ned.
– Jeg fikk kjøpt det resterende som ikke skulle sendes til Tyskland, men hele montasjeavdelingen og en del av verkstedsmaskinene og en del sprøyte-støpe-maskiner skulle sendes til Tyskland. En del havnet også til datterselskaper i Schneider, sier Reberg.
Planen har vært forandret flere ganger
Om Reberg ikke vil røpe nøyaktig hva som skal produseres i de gamle Elko-lokalene, kan han i alle fall røpe at den opprinnelige planen fra 2020 har blitt forandret flere ganger.
– Den gangen hadde jeg en idé om å begynne med egenutvikla produkter. Jeg hadde foreløpige avtaler med andre aktører som hadde egne prosjekter de trengte plastdeler til, sier Reberg.
Men ting gikk ikke like fort som Reberg hadde håpet på den gangen. Han forteller at prosjektet fikk kjepper i hjulene da det ble avgjort at de ikke kunne starte med noen produksjon før det forelå en leieavtale med ny eier. Tiden gikk og oppkjøpet av fabrikken og leieavtalen ble ikke godkjent før desember 2022.
I mellomtiden har Reberg brukt tiden godt likevel.
– Jeg har gått over av alt av maskiner og utstyr slik at de er mest mulig klar for ny produksjon, alt ligger til rette for en rask oppstart, har også brukt mye tid for å finne ut hva jeg faktisk har fått tak i, og mye tid til rydding og sortering, sier Reberg.
Gründerne har også en del utstyr til overs og oppfordrer de som skulle trenge noe til å ta kontakt.
Han forteller at det ikke bare er maskiner for plaststøping, men mye annet teknisk utstyr, verksted-maskiner og masse inventar. I mange måneder har Reberg holdt på for å få orden på ting.
– Før vi kan starter opp, må vi få i havn avtaler, få tak i sprøytestøpe-verktøy og riktige typer plast- råstoff, sier Reberg.
Forskjellige typer plastdeler til flere aktører
Reberg forteller at produksjonen kommer til å innebære litt forskjellige typer plastdeler til flere aktører, men siden de fortsatt er i en prosess, vil han ikke røpe detaljer.
Reberg har vært på jobb i bygget hver dag etter nedleggelsen også.
– Jeg håper å komme i gang med noe produksjonen i løpet av dette året, sier Reberg.
300 grams plastdeler produseres på 200 tonns maskiner
Reberg forteller at de har åtte sprøyte-støpe-maskiner fra 40 tonn til 200 tonn som den største.
– Det setter begrensinger i forhold til arealet på plastdelene som skal produseres og skuddvekten. Det kreves et enormt lukketrykk for å holde formen lukket under støpning, forklarer Reberg.
Nå har de muligheten til å lage plastdeler som veier noen få gram til i overkant av 300 gram. Delen kan ha et ca areal på omtrent 20 x 20 cm. Da er det snakk om arealet/flaten på produktet som blir utsatt for det høye massetrykket inne i formrommet. Men det er mange faktorer som påvirker hvor store deler som kan kjøres, da bruker jeg egne formler for utregning av riktig lukketrykk, det er viktig med riktig lukketrykk i forhold til delen som skal lages.
Store krefter og trykk
Når det enorme masse-trykket (opp til ca 2000bar) under innsprøyting prøver å tvinge formen opp, møter det like enorme krefter fra 40 til 200 tonn/cm2 fra maskinene som holder formhalvdelene igjen, sier Reberg.
Hvis maskinene skulle glippe, får man det som kalles flass. Det betyr at plast tyter ut på steder man ikke ønsker, og skaper arbeid de ikke ønsker i etterkant.
Kilde: Intervju med Plastforum.